Day 1 :
Keynote Forum
Miroslav Piska
Brno University of Technology, Czech Republic
Keynote: Advanced knee implants for the third millennium
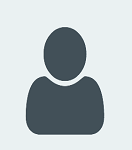
Biography:
Miroslav Piska has completed his PhD from Brno University of Technology University. He is the Director of Institute of Manufacturing Technology in Faculty of Mechanical Engineering from 2003. He has published more than 250 papers in scientific journals and conference proceedings and has been serving as an Editorial Board Member of 4 scientific journals and reviewer of 6 other scientific periodics.
Abstract:
This work deals with today's frequent problem of human joint replacements by applying of advanced radiology techniques (CT, MR, X-ray), application of powder materials and the modern additive (melting of metal powders by electron beam - EBM) and machining technologies. The main attention is devoted to the EBM used by the ARCAM Q10plus machine. A special attention is then paid to the data processing, optimization of design, technological parameters, quality of the produced materials and their post-processing, expressed by 3D topographies of the machined surfaces, machinability, mechanical and tribological properties. The studied technologies include turning, milling, belt grinding and tumbling, in dry conditions. In general, the material exhibits a high resistance to the machining, expressed in terms of specific cutting energies (KISTLER 9575B, Dynoware). Analyses of the samples were made to quantify the production precision and quality (electron microscopy Tescan MIRA 3GM, electron dual microscopy TermoFischer, Alicona IF G6, Mahrvision MM 420) after sintering in different technological modes. The final surface quality results in glossy surfaces (Ra<0.04 um) with high material ratios that enhance the resistance to fatigue crack propagations. The results are very encouraging because this advanced technology (starting at the basic surgical inspections up to the operation with advanced taylor-made implant) can offer an optimized implant that prevails in superior mechanical properties, light mass and excellent mechanical properties. Moreover, a bigger ratio of the original bone can be preserved so a longer life of the implants and reduction of re-operations and after-effects can be expected.
Keynote Forum
Soshu Kirihara
Osaka University, Japan
Keynote: Stereolithographic additive manufacturing of ceramic components
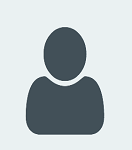
Biography:
Soshu Kirihara is a Professor of Joining and Welding Research Institute (JWRI), Osaka University, Japan. In his main investigation “Materials Tectonics”, geometric structures were successfully fabricated to modulate energy and materials flows effectively. Original stereolithography systems were developed, and new start-up company “SK-Fine” was established through academic-industrial collaboration.
Abstract:
Stereolithographic additive manufacturing (STL-AM) of lamination shaping can fabricate solid components according to topological geometry. Two dimensional (2D) cross sectional patterns were created through photo polymerization by ultra violet laser drawing on spread resin paste including ceramic nanoparticles, and three dimensional (3D) composite models were sterically printed by layer lamination though chemical bonding. An automatic collimeter was equipped with the laser scanner to adjust beam diameter. Fine or coarse beams could realize high resolution or wide area drawings, respectively. As row material of the 3D printing, nanometer sized metal or ceramic particles were dispersed in to photo sensitive liquid resins from 40 to 60% in volume fraction. The resin paste was spread on a glass substrate at 10 μm in layer thickness by a mechanically moved knife edge. An ultraviolet laser beam of 355 nm in wavelength was adjusted from 10 to 300 μm in variable diameter and scanned on the pasted resin surface. Irradiation power was changed automatically from 10 to 200 mW for enough solidification depth for 2D layer bonding. The created 3D composite precursor was dewaxed and sintered in the vacuum and air atmosphere to obtain full metal and ceramic components. Through the computer aided design, manufacture and evaluation (CAD/CAM/CAE), geometrically modulated periodic and self-similar patterns with graded and fluctuated structures were processed. Porous electrode of yttria stabilized zirconia for solid oxide fuel cell, alumina photonic crystals to control electromagnetic waves and artificial bones of calcium phosphate scaffolds were created successfully.
- dvances in 3D Printing & Additive Manufacturing Technology | Innovations in 3D Printing | Design for 3D Printing | 3D Printing Materials | Benefits of 3D Printing and Technology | Future Technology in 3D Printing | Challenges in 3D Printing | 3D printing in Biomaterials | Clinical applications of 3D Printing Innovations | Applications of 3D Printing in healthcare & medicine | Nano 3D Printing
Location: Rome, Italy
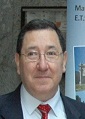
Chair
José L Ocaña
UPM Laser Centre - Polytechnic University of Madrid, Spain
Session Introduction
Srdjan Milenkovic
IMDEA Materials Institute, Spain
Title: Development of Al alloys for additive manufacturing
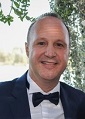
Biography:
Srdjan Milenkovic obtained a PhD in 2002 from the State University of Campinas, Brazil. He joined the Department of Materials Technology at the Max-Planck-Institute for Iron Research (MPIE) in Düsseldorf, Germany, as a Research Associate. Since March 2011, he was appointed as a Head of the Solidification Processing and Engineering group at the IMDEA Materials Institute. His research expertise includes advanced solidification processing techniques with special emphasis on gas atomization of powders for additive manufacturing and development of novel high- throughput casting methods. He has published over 55 papers in JCR journals, among which two in Nano Letters with impact factor
Abstract:
Additive manufacturing (AM) technology is being adopted in more and more industries and the focus of research and development is shifting to the materials in use. However, limited processability of high-performance materials restrict the robustness of the process in some cases, while in other cases the best materials for a given application cannot be processed at all. Currently only a few alloys can be reliably processed by this methodology, and in particular the number of different aluminium alloys available for AM is still rather limited. The main reason is that the strongest Al alloys, which get their strength from precipitation hardening, contain highly volatile elements such as Zn, Mg, etc. leading to turbulent pools, pores and low mechanical properties. This talk will review ongoing research on development of the innovative aluminium alloy specifically designed for SLM. Two different approaches will be presented: on one hand, on tailoring the chemical composition to improve processability, specifically crack susceptibility, of wrought aluminium alloys of the 7xxx series (Al-Zn alloys) to increase mechanical resistance of weldable casting grade AlSi10Mg alloy. A special emphasis will be placed on powder production by gas atomization as a first and an important step in alloy development for additive manufacturing. It will be demonstrated how the desirable compositions can be achieved and what are the main challenges faced. Also the properties of the powders will be assessed and suitability for SLM demonstrated.
A Errachid
UMR 5280-Institut des Sciences Analytiques, CNRS, Université de Lyon, France
Title: A 3D-printed automated sample storage unit for sporadic sampling in innaccessible aquatic environment
Biography:
A Errachid is a Full Professor Classe Exceptionnelle at the University Claude Bernard-Lyon 1 since the end of 2008. He received his PhD degree from the Universitat Autonoma de Barcelona in 1997. Between 1997 and 2001 he worked as Junior Research Scientist at the Centro National de microelectronica (CNM). He later joined the Department of Electronics of University of Barcelona and IBEC as Senior Research, where he worked from 2001 till 2008. He has obtained top-level results in the field of silicon-based (bio)chemical sensors using field-effect transistors and micro/nanoelectrode structures. His deep knowledge and understanding of the electronic devices structure as well as operation and interplay between (bio)chemical molecules and electronics, has resulted in development of novel (bio)sensor devices such as, the original nanosensor device based on olfactory proteins developed under SPOT-NOSED project, amongst others). He has an extensive expertise in EU projects coordination and participation, including KardiaTool (H2020-NMBP-X-KET-2017 no. 768686), HEARTEN (H2020-PHC-26-2014, no. 643694), MicroMole (H2020-FCT-2014, no. 653626), DiagCan (FP7-PEOPLE-2013-IEF, no. 628363), Sea-on-a-Chip (FP7-OCEAN-2013, no. 614168), SMARTCANCERSENS (ICT FP7, no. 294993), and SensorART (ICT-FP7, no, 248763) projects. To date, he has published more over than 195-refereed Scopus papers and his h-index is 28.
Abstract:
Sewage epidemiology has been proven to be a powerful tool to profile a community’s behaviour both in large and small areas. Conventional wastewater analysis is based on manually taken samples, subsequent transport to a specialized lab environment and analysis within a certain period of time. However, due to the high logistic efforts, sampling intervals are usually rather long and can hardly be carried out spontaneously or out of a well-planned sampling campaign. Therefore, automated sampling devices are becoming popular nowadays, as they can be placed on-site in a single operation and be in stand-by mode during long periods of times waiting to be triggered by a predefined sampling protocol. In this context, we report on a miniaturized, low-cost, easy-to-operate and low-power consumption microfluidic automated sampler for sporadic sample collection. The device uses a piezoelectric micropump and three miniaturized electro-valves that are assembled in a 3D-printed microfluidic manifold. Up to three samples can be stored in a 3D-printed single manifold that contains three 2.3 mL reservoirs connected to main body of the device. Moreover, the automated sampler can be remote controlled using a customized control board that enables to trigger the system and set a desired flow rate and time of sampling. Furthermore, its low-power- consumption feature enables the device to be powered through a lithium battery. All these qualities make the automated sample device to be very useful for applications where one or several sporadic samples must be taken in poor accessible environments such as the sewer network without the need of personal presence during the sampling event.
Martin Hannibal
University of Southern Denmark, Denmark
Title: Additive manufacturing in the manufacturing industry – use, developments, & potentials
Time : 12:45-13:15
Biography:
Martin Hannibal is Head of Research in International Business & Entrepreneurship at the Department of Marketing & Management, SDU. His research is focused on knowledge intensive start-ups and additive manufacturing. He is actively involved in international research networks focused on these topics (Academy of International Business). He has published in various high ranking and topic specific peer-reviewed outlets such as International Business Review, Journal of International Marketing, Entrepreneurship & Regional Development, and Journal of International Entrepreneurship. He has been involved in several projects involving industrial partners and has a wide experience in disseminating and discussing research with relevant industrial partners.
Abstract:
Industry 4.0 is epitomized by several emerging technology breakthroughs and represent new ways in which technology becomes embedded within products, services, industries and societies in general. The evidence of dramatic changes caused by some of the constituent technologies of i4.0 such as additive manufacturing (AM) has already been illustrated through numerous business cases. Based on this many authors suggest that entire industries will be disrupted by AM. Many observers have argued that AM will offer numerous opportunities for existing firms and provide a basis for a new generation of start-up firms. The specifics of these opportunities and concrete potentials may be highly dependent on the specific industrial setting. However, empirical research into the details of this still very sparse. To address this gap in literature a survey has been conducted on Danish manufacturing firms. The survey tracked in which domain – prototyping, production support, or finished products – AM is currently used. Our research shows, a primary use of AM in prototyping and product development processes as well as a broad use in production support – grippers, fixtures, tools etc. Our research indicates that ownership coupled with multi-domain use of AM is a key driver to both business development in general and development of new products and services. The research indicates this potential of AM is not dependent on size of the firm implementing the technology.
Andrew J Kobets
Children's Hospital at Montefiore, USA
Title: Virtual modeling, stereolithography, and intraoperative CT guidance for the optimization of sagittal synostosis reconstruction
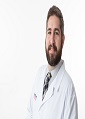
Biography:
Andrew J Kobets is currently Chief Resident of Neurosurgical Resident at Montefiore Medical Center and is working on a translational research project as a Visiting Scientist at both the Feinstein Institute for Medical Research at Northwell Health and at the Albert Einstein College of Medicine. He has initiated and overseen the initiation of three clinical trials in the Department of Neurological Surgery at Montefiore Medical Center and is the first utilizing MR Elastography to evaluation shunt function in New York. He graduated from the Yale School of Medicine with a medical degree and a Master’s in Health Sciences. He studied Systems Neuroscience at the Johns Hopkins University as an Undergraduate and will return to Johns Hopkins after residency for a Fellowship in Pediatric Neurosurgery.
Abstract:
Objective: Sagittal synostosis affects 1 in 1000 live births and may result in increased intracranial pressure, hindrance of normal neural development, and cosmetic deformity due to scaphocephaly. Historically, several approaches have been utilized for surgical correction and recently, computed tomography (CT)-guided reconstruction procedures are increasingly used. In this report, the authors describe the use of a CT-derived virtual and stereolithographic (3D printed) craniofacial models, which are used to guide intraoperative bone placement, and intraoperative CT guidance for confirmation of bone placement, to ensure the accuracy of surgical correction of scaphocephaly, as demonstrated to parents.
Methods: Preoperative high-resolution CT imaging was used to construct 3D image sets of the skulls of two infants (a 14-month-old female and a 6-month-old male) with scaphocephaly. These 3D image sets were then used to create a virtual model of the proposed surgical correction for each of the infants’ deformities, which was then printed and made available for use intra-operatively to plan the bone flap, fashion the bone cuts, and optimize graft placement. After the remodeling, adherence to the preoperative plan was assessed by overlaying a CT scan of the remodeled skull with the virtual model. Deviations from the preoperative model were noted.
Findings: Both patients had excellent postoperative cosmetic correction of head shape and contouring. The mean operative time was 5 h, blood loss was 100 ml, and one child required modification of the subocciput after intraoperative imaging showed a deviation of the reconstruction from the surgical goal as depicted by the preoperative model.
Conclusion: The addition of neuro-navigation to stereolithographic modeling ensured the accuracy of the reconstruction for our patients and provided greater confidence to both surgeons and parents. While unisutural cases are presented for clarity, correction was still required for one patient. The cost of the models and the additional CT required must be weighed against the complexity of the procedure and possibly reserved for patients with potentially complicated corrections.
Konrad Gruber
Wrocław University of Science & Technology, Poland
Title: The methodology of selective laser melting process development
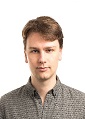
Biography:
Konrad Gruber is a specialist in additive manufacturing and material engineering. Since 2014, he works as a research assistant and PhD candidate at the Centre for Advanced Manufacturing Technologies (CAMT-FPC) of Wrocław University of Science and Technology, where he conducts research in the field of metal additive manufacturing (SLM, EBM). He is a participant of R&D projects performed for aviation and energy industries. His doctoral dissertation is carried out in the field of AM production of nickel alloys parts for the applications in thin-walled aircraft engine structures.
Abstract:
Nowadays trends on manufacturing technologies market, as well as growing requirements especially from the specialist industry such as aviation, create new challenges for designers and producers, which result in the necessity of modifying properties of materials and structural components. One of the possibilities to influence these properties is application of additive technologies (e.g. selective laser melting - SLM) for production of prototype models, pre-production and production series, finished products, possibly with internal spatial structures, which in a significant way change tribological properties, resistance to mechanical loads, operational durability, as well as resistance to unfavorable and hard working conditions. The essential factors determining the definition of a given technology as the future-oriented and worth of developing are the achieved features of the worked shapes and surfaces, costs of its implementation and use, elasticity and care for the natural environment. SLM is a fast growing technology, which creates opportunities for manufacturing complex geometries (both monolithic volumes and spatial structures) directly from metal powders and CAD 3D models. Therefore, the SLM technology is recognized as a manufacturing technology of the future. Many industry leaders are implementing SLM into their production standards, e.g.: automotive, aviation, space and medicine companies. SLM technology can also be used for the development of new materials, through the possibility of manufacturing elements from various mixtures of metal powders. The methodology presented in this article allows expanding the use of SLM in a wide range of industries and tests the properties of new materials on functional parts and 3D specimens.
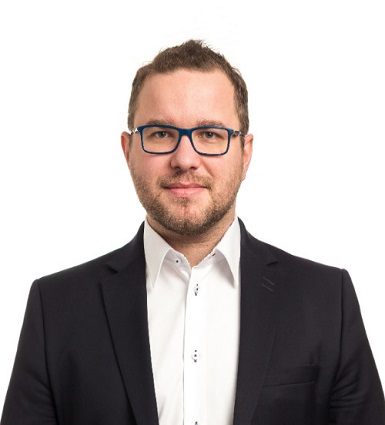
Biography:
saf
Abstract:
sdf