Day 1 :
Keynote Forum
Montaser LM
Menoufia University, Egypt
Keynote: 3D printing technology application for tissue engineering
Time : 09:30-10:00
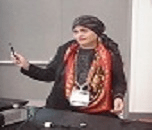
Biography:
Laila M. Montaser MD is a distinguished Prof. of Clinical Pathology. Chair Stem Cell, Regenerative Medicine, Nanotechnology and Tissue Engineering (SRNT) Research Group. She served as the Chair, Founder leader of Clinical Pathology Department, Faculty of Medicine, Menoufia University, Egypt. Prof. Montaser an internationally recognized stem cell technology and regenerative medicine professional is a transformational leader and original thinker who is responsive to change. She has key competence in stem cell technology and regenerative medicine policy reinforced by global level and international experience in research, formulation and capacity building. She gained three Awards: Medal of Merit for the ideal Doctor from Egyptian Medical Syndicate in 1986, 1998, and 2002. In 2020-2021, she was awarded twenty certificates of appreciation for successfully presenting thirty six Global Webinars (55.6%) for outstanding contribution to the commitment to provide continuing education to the international community from her home office amid the lock-down of COVID-19 crisis.
Abstract:
Statement of the Problem: Patients with organ failure often suffer from increased morbidity and decreased quality of life. Current strategies of treating organ failure have limitations, including shortage of donor organs, low efficiency of grafts, and immunological problems. So, evolution of novel technicalities in biomedical engineering has aided to promote numerous prospects for modern stands for transplant trials.Methodology & theoretical orientation: 3D printing is emerging as a powerful tool for tissue engineering by enabling 3D cell culture within complex 3D bio-mimetic architectures. Bio printing is an eliciting device for distinguishing stem cells in 3D styles. The use of proper bio-materials with its cross-linking feature on extension of a cross linker allows the perfect building with which we can cultivate stem cells into a certain tissue or organ.Findings: Recent advances have enabled 3D printing of biocompatible materials, cells and supporting components into complex 3D functional living tissues. Bio-printing harnesses three dimensional precipitations of cell loaded bio-materials to originate an orderly fabric with tissue suitable building. This kind of engineered organ can display substitutes to donors for organ transplantation and tissue printing could show superior clinical rating of therapeutic factors. Nano-bio-materials function a crucial part in fostering the physicochemical characteristics of subsisting bio-materials. 3D-bioprinted tissue constructs are being developed not only for transplantation but also for use in drug discovery, analysis of chemical, biological, and toxicological agents.
Keynote Forum
Yuan Chen
The University of Sydney, Australia
Keynote: 3D-printed continuous and short carbon fibre reinforced composite metamaterials with tailorable negative Poisson’s ratios
Time : 10:00 - 10:30
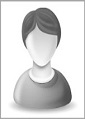
Biography:
Dr. Yuan Chen is currently undertaking a Research Fellow position as ARC Postdoctoral Research Associate in the University of Sydney. He obtained his PhD from the University of Sydney in 2019. His research interests are concentrated on additive manufacturing of composite materials, design and computational analysis of composite structures, topological and structural optimisation for metamaterials and advanced composites. Due to his achievements, he has been invited to give speeches and chair sessions at various academic seminars and prestigious international conferences, and he has also received several awards such as Young Scientist Award, Best Oral Presentation, etc. Currently, he is a professional member of several renowned academic societies and organisations, such as Royal Aeronautical Society (RAeS), American Institute of Aeronautics and Astronautics (AIAA), European Mechanics Society, etc
Abstract:
Currently, metamaterials have been attracting increasing attention with a wide range of applications, i.e., smart materials, graded materials, shape memory alloys, biomaterials, etc. This study developed an integrated computational design method with 3D printing to endow continuous and short carbon fibre reinforced composite metamaterials with negative Poisson’s ratios. First, continuous carbon fibre (CCF) composites were designed using a multidisciplinary technique integrating homogenisation-based topology optimisation and fibre placement methodology for determining the 3D printing set-up with fused filament fabrication. Second, specimens made of pure polyamide (PA), short carbon fibre reinforced PA (SCF/PA) and CCF reinforced PA (CCF/PA) were fabricated and tested for a comparative evaluation. Lastly, the effects of carbon fibre reinforcement were investigated, showing that a small addition of CCFs (vol% = 0.23) can improve the negative Poisson’s ratio from −0.24 of the PA metamaterials to −0.34. However, other greater CCF volume fraction would reduce the negative Poisson’s ratio.
Keynote Forum
Trivedi Achyut
Ganpat University, India
Keynote: Current challenges and adoption of Additive Manufacturing technology in Industrial sector
Time : 10:30-11:00
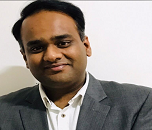
Biography:
"3D printing has huge research challenges and young graduates always find better solutions for the same” is the philosophy of Prof. Achyut Trivedi. He is an academic professional and researcher in the field of most promising technology that is "3D printing". Currently Prof. Achyut Trivedi working in Ganpat University as Head of GUNI Additive Manufacturing (3D Printing) technology Centre of Excellence. He aims at imparting education that enhances and enriches the intellect, noble, imaginative and creative self that lies deep within an individual. He follows different teaching pedagogies, more specifically Blended Learning. He is committed in taking constructive and purposeful actions to create optimistic and independent graduates, who will bring glory to the society at large. He has attended several conference and workshops in the field of 3D printing. He is also jointly working with orthopaedic society for 3D printing medical application. Research interest of Mr. Achyut included bio-manufacturing, new materials for FDM, drug- manufacturing. He is also member of professional bodies like SAE, ASTM, IAENG, ISTE.
Abstract:
Statement of Problem: Additive Manufacturing, popularly known as 3D Printing considers an essential element of the Industrial Revolution 4.0 mission. Despite having many advantages from traditional manufacturing like low material wastage, fast production time, ease of operation, etc. AM still constraints with limited use. Apart from the theoretical advantage of AM, there are still in-depth studies required to incorporate AM technology into the industrial sector. The present study mainly focused on the various challenges of adopting AM technology in the industrial sector. The study also aims to provide possible solutions to overcome the same. Methodology: Detailed literature survey and state art of research has been conducted to frame the possible solutions. Interactions with many industrial leaders using questionnaire techniques to identify the challenges at their levels. Findings: The AM technology still lack of many challenges like standardization to incorporate into industries. The technology is mainly prototyping driven hence still there are challenges for final part production using AM. Conclusion & Significance: Utilization of Additive Manufacturing in industrial sector still requires many challenges to addresses. The present study addressed the current challenges and respective recommendations are frames to incorporate AM technologies into Industrial sectors.
Keynote Forum
Hamidreza Mosleh
University of Medical Sciences, Iran
Keynote: Using 3D printing for pre-planning of High Tibial Osteotomy
Time : 11:00-11:30
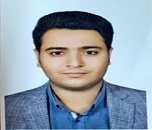
Biography:
Hamidreza Mosleh has 24 years old and he is a MSc student of Anatomical sciences at Iran university of medical sciences. His research interests include anthropology and radiology in anatomy
Abstract:
Recent developments in 3D printing have gave orthopedic surgeons among a novel technology that has the ability to revolutionize preoperative planning. The appearance of 3D printing technology enables the digital preoperative plan and simulation to move from the virtual phase to the reality phase. Varum disorders are recurrent lower limb malformations associated with many anatomical changes in the knee joint and adjacent segment. High Tibial osteotomy is one of the best treatment options in genuvarus deformity. In this randomized clinical trial study, 16 patients with genuvarum were selected that divided between the 2 groups (main study and the control group). A standing alignment radiograph were taken from all patients to measure mMPTA, mLDFA, CA and mFTA. CT scan was taken from 8 patients in the main study group. Mimics software was used to build the 3D model. Then, we had to prepare the model made for printing by a 3D printer. Finally, the printed 3D model is provided to the orthopeadic surgeon. So, the surgeon operated on half of the patients with the help of a printed 3D model. Orthoped performed an osteotomy on the printed model that was exactly the same as the actual surgery After the surgery, we once again took radiography (all patients) and a CT scan (main study group). The aim is to see if the angles have been corrected after surgery. Finally, a comparison was made between these two surgical procedures. Results showed that the printed 3D model group had lower: 1. cost of hospitalization and anesthesia, 2. duration of surgery, 3. fluoroscopic dose and 4. bleeding.
Keynote Forum
H. YAAGOUBI
Mohammed V University, Morocco
Keynote: Theoretical study of selective laser sintering of polyamide 12
Time : 11:30-12:00
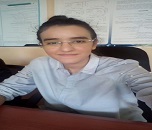
Biography:
Hanane YAAGOUBI : was born in morocco on 24th april 1992. state engineer diploma (mechanical design and innovation) , FST FES, sidi mohamed ben abdellah university in FES and she is currently a PHD student in the laboratory of applied mechanics and technologies ( LAMAT), ENSET,STIS research center mohammed V university-Rabat, Morocco , Her research is focused on printing 3D.
Abstract:
The laser sintering process allows to create a wide range of parts printed in 3 dimensions (3D). 3D printing is done layer by layer on powders (plastics, juices, polymers), using a laser. SLS printing requires the use of a special gas, nitrogen, SLS 3D printers are made from two enhancement chambers The laser draws the case of each region of the 3D drawing on a bed of powder. Each time a diaper is made, the bed breaks and another diaper is made over the previous layers The bed continues to descend until the last layer is formed and the part is complete, one of the fundamental points of interest of SLS is that it does not need the help structures used by many people. many other manufacturing innovations of added substances to prevent the plane from falling off during creation. The article rests on a bed of powder, no help is fundamental SLS innovation really stands out when you need durable plastic parts. It is equipped to deliver fully solid parts suitable for real life testing and mold making, while other added substance production strategies can become tricky after a while; so mathematical modeling to properly optimize this process is necessary.